
微信公眾號二維碼
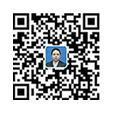
微信咨詢顧問二維碼
精益生產(chǎn)是當(dāng)今世界先進(jìn)的管理方法,首先由日本豐田公司提出,現(xiàn)已被廣泛應(yīng)用于工業(yè)制造業(yè)中,那么該如何開展呢?
一、精益生產(chǎn)的含義
精益生產(chǎn)(Lean Production,簡稱LP)是美國麻省理工學(xué)院數(shù)位國際汽車計(jì)劃組織(IMVP)的專家對日本“豐田JIT(Just In Time)生產(chǎn)方式”的贊譽(yù)之稱,精,即少而精,不投入多余的生產(chǎn)要素,只是在適當(dāng)?shù)臅r(shí)間生產(chǎn)必要數(shù)量的市場急需產(chǎn)品(或下道工序急需的產(chǎn)品);益,即所有經(jīng)營活動(dòng)都要有益有效,具有經(jīng)濟(jì)性。精益生產(chǎn)是當(dāng)前工業(yè)界最佳的一種生產(chǎn)組織體系和方式。
精益生產(chǎn)的特點(diǎn)是消除一切浪費(fèi),追求精益求精和不斷改善。去掉生產(chǎn)環(huán)節(jié)中一切無用的東西,每個(gè)工人及其崗位的安排原則是必須增值,撤除一切不增值的崗位。精簡是它的核心,精簡產(chǎn)品開發(fā)設(shè)計(jì)、生產(chǎn)、管理中一切不產(chǎn)生附加值的工作,旨在以最優(yōu)品質(zhì)、最低成本和最高效率對市場需求作出最迅速的響應(yīng)。
二、精益生產(chǎn)的優(yōu)勢及意義
與大量生產(chǎn)方式相比,日本所采用的精益生產(chǎn)方式的優(yōu)越性主要表現(xiàn)在以下幾個(gè)方面:
1、所需人力資源--無論是在產(chǎn)品開發(fā)、生產(chǎn)系統(tǒng),還是工廠的其他部門,與大量生產(chǎn)方式下的工廠相比,最低能減至1/2;
2、新產(chǎn)品開發(fā)周期—最低可減至l/2或2/3;
3、生產(chǎn)過程的在制品庫存—最低可減至大量生產(chǎn)方式下一般水平的1/10;
4、工廠占用空間—最低可減至采用大量生產(chǎn)方式下的1/2;
5、成品庫存—最低可減至大量生產(chǎn)方式下平均庫存水平的1/4;
精益生產(chǎn)方式是徹底地追求生產(chǎn)的合理性、高效性,能夠靈活地生產(chǎn)適應(yīng)各種需求的高質(zhì)量產(chǎn)品的生產(chǎn)技術(shù)和管理技術(shù),其基本原理和諸多方法,對制造業(yè)具有積極的意義。精益生產(chǎn)的核心,即關(guān)于生產(chǎn)計(jì)劃和控制以及庫存管理的基本思想,對豐富和發(fā)展現(xiàn)代生產(chǎn)管理理論也具有重要的作用。
精益生產(chǎn)的支柱與終極目標(biāo)
“零浪費(fèi)”為精益生產(chǎn)終極目標(biāo),具體表現(xiàn)在PICQMDS七個(gè)方面,目標(biāo)細(xì)述為:
(1)“零”轉(zhuǎn)產(chǎn)工時(shí)浪費(fèi)(Products•多品種混流生產(chǎn))
將加工工序的品種切換與裝配線的轉(zhuǎn)產(chǎn)時(shí)間浪費(fèi)降為“零”或接近為“零”。
(2)“零”庫存(Inventory•消減庫存)
將加工與裝配相連接流水化,消除中間庫存,變市場預(yù)估生產(chǎn)為接單同步生產(chǎn),將產(chǎn)品庫存降為零。
(3)“零”浪費(fèi)(Cost•全面成本控制)
消除多余制造、搬運(yùn)、等待的浪費(fèi),實(shí)現(xiàn)零浪費(fèi)。
(4)“零”不良(Quality•高品質(zhì))
不良不是在檢查位檢出,而應(yīng)該在產(chǎn)生的源頭消除它,追求零不良。
(5)“零”故障(Maintenance•提高運(yùn)轉(zhuǎn)率)
消除機(jī)械設(shè)備的故障停機(jī),實(shí)現(xiàn)零故障。
(6)“零”停滯(Delivery•快速反應(yīng)、短交期)
最大限度地壓縮前置時(shí)間(Lead time)。為此要消除中間停滯,實(shí)現(xiàn)“零”停滯。
(7)“零”災(zāi)害(Safety•安全第一)
三、精益生產(chǎn)之管理工具—Kanban
Kanban作為精益生產(chǎn)的一種核心管理工具,可對生產(chǎn)現(xiàn)場進(jìn)行可視化管理。一旦出現(xiàn)異常可在第一時(shí)間通知相關(guān)人員并采取措施解除問題。
四、精益生產(chǎn)中的看板管理在生產(chǎn)過程的作用
1)主生產(chǎn)計(jì)劃:看板管理的理論中不涉及如何編制和維護(hù)主生產(chǎn)計(jì)劃,它是以一個(gè)現(xiàn)成的主生產(chǎn)計(jì)劃作為開端的。所以采用準(zhǔn)時(shí)化生產(chǎn)方式的企業(yè)需要依靠其他系統(tǒng)來制訂主生產(chǎn)計(jì)劃。
2)物料需求計(jì)劃:雖然采用看板管理的企業(yè)通常將倉庫外包給供應(yīng)商管理,但是仍然需要向供應(yīng)商提供一個(gè)長期、粗略的物料需求計(jì)劃。一般的做法是按照一年的成品銷售計(jì)劃得出原材料的計(jì)劃用量,同供應(yīng)商簽訂一攬子訂單,具體的需求日期和數(shù)量則完全由看板來體現(xiàn)。
3) 能力需求計(jì)劃:看板管理不參與制訂主生產(chǎn)計(jì)劃,自然也就不參與生產(chǎn)能力需求計(jì)劃。實(shí)現(xiàn)看板管理的企業(yè)通過工序設(shè)計(jì)、設(shè)備布置、人員培訓(xùn)等手段來實(shí)現(xiàn)生產(chǎn)過 程的均衡化,從而大大減少了生產(chǎn)過程中的能力需求不平衡的現(xiàn)象??窗骞芾砜梢院芸斓乇┞冻瞿芰^?;虿蛔愕墓ば蚧蛟O(shè)備,然后通過不斷地改進(jìn)來消除問題。
4) 倉庫管理:為了能解決倉庫管理的難題,往往采用將倉庫外包給供應(yīng)商管理的方法,要求供應(yīng)商必須能隨時(shí)提供所需的物料,在生產(chǎn)線領(lǐng)取物料的同時(shí)才發(fā)生物料所 有權(quán)轉(zhuǎn)移。這實(shí)質(zhì)上是將庫存管理的包袱丟給供應(yīng)商,由供應(yīng)商承擔(dān)庫存資金占用的風(fēng)險(xiǎn)。這樣做的前提條件是與供應(yīng)商簽訂長期一攬子訂單,供應(yīng)商減少了銷售風(fēng) 險(xiǎn)和費(fèi)用,也就愿意承擔(dān)庫存積壓的風(fēng)險(xiǎn)了。
5)生產(chǎn)線在制品管理:實(shí)現(xiàn)準(zhǔn)時(shí)化生產(chǎn)方式的企業(yè)在制品數(shù)量被控制在看板數(shù)量之內(nèi),關(guān)鍵在于確定一個(gè)合理有效的看板數(shù)量。
以上是對精益生產(chǎn)方式的介紹,精益生產(chǎn)只是一種生產(chǎn)方式,如需真正實(shí)現(xiàn)其終極目標(biāo)(上面所說的7個(gè)“零”。),就必須借助些現(xiàn)場管理工具,如看板、Andon系統(tǒng)等,利用這些工具可做可視化管理,能在問題出現(xiàn)的第一時(shí)間就能采取措施解除影響,從而保證整個(gè)生產(chǎn)處于正常生產(chǎn)的狀態(tài)。
五、精益生產(chǎn)方式有哪些?
1、5S與目視控制
“5S”是整理(Seiri) 、整頓(Seiton) 、清掃(Seiso) 、清潔(Seikeetsu)和素養(yǎng)(Shitsuke)這5個(gè)詞的縮寫 ”5S” ,起源于日本。5S是創(chuàng)建和保持組織化,整潔和高效工作場地的過程和方法,可以教育、啟發(fā)和養(yǎng)成良好“人性”習(xí)慣,目視管理可以在瞬間識別正常和異常狀態(tài),又能快速、正確的傳遞訊息。兩天的課程可以幫助學(xué)員:
• 了解為什么要做5S,掌握推行5S和目視管理的步驟和方法 ;
• 了解視覺控制工具的類型,學(xué)會(huì)如何創(chuàng)建視覺控制工具以及一些最基本的可以快速改進(jìn)所有工作區(qū)域的新工具。
2、準(zhǔn)時(shí)化生產(chǎn)(JIT)
準(zhǔn)時(shí)生產(chǎn)方式是起源于日本豐田汽車公司,其基本思想是“只在需要的時(shí)候,按需要的量生產(chǎn)所需的產(chǎn)品” 。這種生產(chǎn)方式的核心是追求一種無庫存的生產(chǎn)系統(tǒng),或使庫存達(dá)到最小的生產(chǎn)系統(tǒng)。
• 認(rèn)識增值與非增值活動(dòng),減少或消除非增值和浪費(fèi) ;
• 七種浪費(fèi)的識別以及最終消除浪費(fèi);
• 學(xué)會(huì)運(yùn)用各種拉動(dòng)方式實(shí)現(xiàn)準(zhǔn)時(shí)化生產(chǎn)。
3、看板管理( Kanban )
Kanban是個(gè)日語名詞,表示一種掛在或貼在容器上或一批零件上的標(biāo)簽或卡片,或流水線上各種顏色的信號燈、電視圖象等??窗迨强梢宰鳛榻涣鲝S內(nèi)生產(chǎn)管理信息的手段??窗蹇ㄆ喈?dāng)多的信息并且可以反復(fù)使用。常用的看板有兩種:生產(chǎn)看板和運(yùn)送看板 。
• 介紹拉動(dòng)系統(tǒng)看板以及用于管理過程的目視化看板,以及這些看板對于生產(chǎn)組織,標(biāo)準(zhǔn)化作業(yè)以及持續(xù)改善的重要意義;
• 生產(chǎn)看板的作用就是購買的“資金”,你需要關(guān)注的是生產(chǎn)過程中你要“購”什么,什么時(shí)候買,買多少。
4、零庫存管理
工廠的庫存 管理是供應(yīng)鏈的一環(huán),也是最基本的一環(huán)。就制造業(yè)而言,加強(qiáng)庫存管理,可縮短并逐步消除原材料、半成品、成品的滯留時(shí)間,減少無效作業(yè)和等待時(shí)間,防止缺貨,提高客戶對 “ 質(zhì)量、成本、交期 ” 三大要素的滿意度。
• 了解庫存管理的基本概念,掌握庫存分析的方法,學(xué)會(huì)選擇合適的庫存系統(tǒng);
• 學(xué)習(xí)、掌握管理庫存作業(yè)的技能;
• 掌握庫存作業(yè)管理表單、程序的制作與實(shí)施技巧。
5、全面生產(chǎn)維護(hù)( TPM )
TPM起源于日本, 是以全員參與的方式,創(chuàng)建設(shè)計(jì)優(yōu)良的設(shè)備系統(tǒng),提高現(xiàn)有設(shè)備的利用率,實(shí)現(xiàn)安全性和高質(zhì)量,防止故障發(fā)生,從而使企業(yè)達(dá)到降低成本和全面生產(chǎn)效率的提高。
• 理解5S與TPM 的關(guān)系;
• 掌握OEE的計(jì)算和如何改善OEE;
• 掌握實(shí)施TPM 的方法 ;
• 如何建立和維護(hù)設(shè)備的歷史記錄,評價(jià)目前的TPM 水平。
6、運(yùn)用價(jià)值流圖來識別浪費(fèi)
生產(chǎn)過程中到處充斥著驚人的浪費(fèi)現(xiàn)象,價(jià)值流圖(Value Stream Mapping)是實(shí)施精益系統(tǒng)、消除過程浪費(fèi)的基礎(chǔ)與關(guān)鍵點(diǎn)。
• 發(fā)現(xiàn)過程中何處產(chǎn)生浪費(fèi) , 識別精益的改進(jìn)機(jī)會(huì);
• 認(rèn)識價(jià)值流的構(gòu)成因素與重要性;
• 掌握實(shí)際繪制“價(jià)值流圖”的能力;
• 認(rèn)識數(shù)據(jù)在價(jià)值流圖示中的應(yīng)用,通過數(shù)據(jù)量化改善機(jī)會(huì)的次序。
7、生產(chǎn)線平衡設(shè)計(jì)
由于流水線布局不合理導(dǎo)致生產(chǎn)工人無謂地移動(dòng),從而降低生產(chǎn)效率;由于動(dòng)作安排不合理、工藝路線不合理,導(dǎo)致工人三番五次地拿起或放下工件。
• 能夠設(shè)計(jì)和實(shí)施一個(gè)線平衡的生產(chǎn)線 ;
• 了解典型流程環(huán)境中的問題及如何影響那些問題 ;
• 知道何時(shí)使生產(chǎn)率最大化。
8、拉系統(tǒng)與補(bǔ)充拉系統(tǒng)
所謂拉動(dòng)生產(chǎn)是以看板管理為手段,采用“取料制”即后道工序根據(jù)“市場”需要進(jìn)行生產(chǎn),對本工序在制品短缺的量從前道工序取相同的在制品量,從而形成全過程的拉動(dòng)控制系統(tǒng),絕不多生產(chǎn)一件產(chǎn)品 。 JIT需要以拉動(dòng)生產(chǎn)為基礎(chǔ),而 拉系統(tǒng)操作是精益生產(chǎn)的典型特征。精益追求的零庫存,主要通過拉系統(tǒng)的作業(yè)方式實(shí)現(xiàn)的。
• 理解拉系統(tǒng)和補(bǔ)充拉系統(tǒng)的定義 ;
• 理解拉系統(tǒng)的關(guān)鍵參數(shù)及計(jì)算方法 ;
• 如何在多變的環(huán)境中將拉系統(tǒng)應(yīng)用于精益項(xiàng)目 ;
• 了解制造拉系統(tǒng)和采購拉系統(tǒng)的區(qū)別。
9、降低設(shè)置時(shí)間 (Setup Reduction)
為了使停線等待浪費(fèi)減為最少,縮短設(shè)置時(shí)間的過程就是逐步去除和減少所有的非增值作業(yè),并將其轉(zhuǎn)變?yōu)榉峭>€時(shí)間完成的過程。 精益生產(chǎn)是通過不斷消除浪費(fèi)、降低庫存、減少不良、縮短制造周期時(shí)間等具體要求來實(shí)現(xiàn)的,降低設(shè)置時(shí)間是幫助我們達(dá)到這一目標(biāo)的關(guān)鍵手法之一。
• 理解設(shè)置時(shí)間是如何影響流程的周轉(zhuǎn)效率 ;
• 學(xué)習(xí)降低設(shè)置時(shí)間的 4 大步驟 ;
• 理解為了降低設(shè)置時(shí)間的必須準(zhǔn)備工作。
10、單件流
JIT是精益生產(chǎn)的終極目標(biāo),它是通過不斷消除浪費(fèi)、降低庫存、減少不良、縮短制造周期時(shí)間等具體要求來實(shí)現(xiàn)的。單件流是幫助我們達(dá)到這一目標(biāo)的關(guān)鍵手法之一。我們需要了解:
• 單件流與傳統(tǒng)作業(yè)的根本差異 ;
• 設(shè)計(jì)如何實(shí)現(xiàn)單件流 ;
通過單件流,您企業(yè)將得到如下益處:
• 不良狀況明顯顯露,及時(shí)解決 ;
• 形成團(tuán)隊(duì)驅(qū)動(dòng),作業(yè)人員集中精力 ;
• 縮短解決問題的時(shí)間 ;
• 作業(yè)人員作業(yè)時(shí)間增加,輔助時(shí)間減少 ;
• 縮小生產(chǎn)面積物流搬運(yùn)減少生產(chǎn)效率提高 。
11、持續(xù)改善 (Kaizen)
Kaizen是個(gè)日語名詞,相當(dāng)于CIP。當(dāng)開始精確地確定價(jià)值,識別價(jià)值流,使為特定產(chǎn)品創(chuàng)造的價(jià)值的各個(gè)步驟連續(xù)流動(dòng)起來,并讓客戶從企業(yè)拉動(dòng)價(jià)值時(shí),奇跡就開始出現(xiàn)了。
• 何時(shí)需要改善( Kaizen ),如何應(yīng)用改善( Kaizen );
• 改善( Kaizen )的策略,常用工具和技巧。
建立生產(chǎn)有序、管理順暢,操作規(guī)范,士氣高昂、高質(zhì)量、低成本、短交期的作業(yè)現(xiàn)場;
為企業(yè)規(guī)劃設(shè)計(jì)一套由內(nèi)到外的形象升級,外觀視覺價(jià)值體現(xiàn)、內(nèi)在的管理內(nèi)涵體現(xiàn);
全員參與設(shè)備管理高產(chǎn)出和低成本運(yùn)營,提升設(shè)備管理能力,維護(hù)能力,提高效率
構(gòu)建班組生產(chǎn)管理體系、循環(huán)評價(jià)、人才育成、持續(xù)改善、績效管理、文化養(yǎng)成體系;
提高產(chǎn)品質(zhì)量、降低生產(chǎn)成本、縮短交期、增加利潤,讓管理更系統(tǒng)科學(xué),執(zhí)行力更強(qiáng)
對工廠的各個(gè)組成部分進(jìn)行合理安排,以提高生產(chǎn)效率、降低成本、優(yōu)化物流、改善工作環(huán)境等