
微信公眾號二維碼
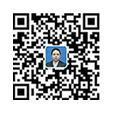
微信咨詢顧問二維碼
近年來TPM推行已經(jīng)在全國大范圍開展,特別是制造業(yè)工廠車間,精益生產(chǎn)咨詢公司在這里所談的不針對任何對象,就談?wù)劷陙砥髽I(yè)在TPM推行上的一些建議而已。
TPM管理推行
TPM是指全員生產(chǎn)性保全活動,TPM工作是為了更好的落實設(shè)備工裝維護、管理工作,響應(yīng)公司TPM小組推進目標(biāo),形成全員參與的良好氛圍,切實做好設(shè)備、工裝日常保養(yǎng)、維護,減少或防止設(shè)備、工裝突發(fā)故障發(fā)生,保持和恢復(fù)設(shè)備、工裝精度和性能,提升設(shè)備、工裝狀態(tài)和管理水平,保持生產(chǎn)順利進行。TPM的八大支柱是:個別改善、自主保全、專業(yè)保全、開發(fā)管理、品質(zhì)保全、人才培養(yǎng)、事務(wù)改善、環(huán)境改善。
TPM活動的6S是整理、整頓、清掃、清潔、素養(yǎng)、安全。以6S為切入點,開展TPM活動。6S是TPM活動的基礎(chǔ),是TPM活動的突破口;6S同樣要程序、規(guī)范管理:確定區(qū)域、人員、標(biāo)準(zhǔn)、周期、方法,并有檢查評估方案;6S中必然發(fā)現(xiàn)根源性的問題——引入清除六源內(nèi)容。TPM的尋找和清除“六源”活動,“六源”為污染源、浪費源、故障源、缺陷源、事故危險源、清掃困難源。
公司開展TPM自主保全活動展開的五大階段:
1)、初期清掃(清掃點檢)
2)、發(fā)生源、困難處的對策
3)、總點檢
4)、點檢效率化
5)、自主管理。
第一階段:初期清掃
1、初期清掃的目的:①以設(shè)備本體為中心的垃圾、塵埃、污染徹底排除。②防止強制劣化。③透過清掃找出潛在缺陷,并予顯現(xiàn)及處置。
2、經(jīng)由清掃接觸設(shè)備的各部位(看、摸),可發(fā)現(xiàn)部位的不良點有振動、發(fā)熱、松動、癥兆。
3、初期清掃的要求:①要將看得見和看不見的地方都清掃干凈;②對清掃工作要進行規(guī)范化管理,制定清掃標(biāo)準(zhǔn),并按標(biāo)準(zhǔn)實施清掃;③長期堅持不懈,把清掃工作當(dāng)作日常工作的一部分,持續(xù)實施。
4、對設(shè)備的清掃必需做到操作工人自己動手,且進行全面清掃,維修人員對清掃活動進行技術(shù)支持。
5、經(jīng)常為設(shè)備清掃是發(fā)現(xiàn)設(shè)備微小問題和變化,從而預(yù)防大問題、嚴(yán)重故障出現(xiàn)的最實用方法;
第二階段:發(fā)生源、困難處的對策
1、TPM第二階段的主要內(nèi)容是發(fā)生源及困難部位改善對策。TPM第二階段的目的是:改善垃圾、污垢、污染的發(fā)生源,飛散的防止或清掃、加油、點檢的困難處所,以縮短清掃、加油、點檢時間和學(xué)習(xí)設(shè)備改善的思考方法,以提升實質(zhì)的效果。
2、清掃困難源指需要清掃,難于清掃,源于速、熱、電、位等。
3、故障源指引起故障的設(shè)備外部和本身條件。
4、危險源指存在安全隱患的現(xiàn)場和設(shè)備狀況。
5、缺陷源指引起產(chǎn)品缺陷的設(shè)備問題及環(huán)境因素。
6、浪費源指造成物、能、人工浪費的人-機系統(tǒng)因素和生產(chǎn)現(xiàn)場。
7、發(fā)生源及困難部位改善對策的作用:使操作員工更加熟悉自己的設(shè)備、改善設(shè)備的使用性能、一勞永逸,同類污染現(xiàn)象不再發(fā)生、培養(yǎng)員工改善的意識和解決問題的能力
8、發(fā)生源及困難部位改善對策的推進要點:突破現(xiàn)狀,大家動手;引入競爭,激發(fā)創(chuàng)意;維護成果,中層引導(dǎo)。
第三階段:總點檢
1、總點檢:是指對設(shè)備操作者在設(shè)備的自主保全方面提出更高的要求,要求操作者更深一層學(xué)習(xí)和掌握設(shè)備的結(jié)構(gòu)、性能、運作原理,以求對設(shè)備進行更加精細的點檢,消除潛在問題,使設(shè)備回復(fù)到初始狀態(tài)的日常點檢活動。
2、總點檢的作用:1降低設(shè)備的故障率;2清除設(shè)備的微缺陷;3全面提升員工的自主保全能力。
3、總點檢的重點在于測量設(shè)備的劣化程度并采取改進措施,是對“事前預(yù)防”中遺漏的問題和結(jié)果的“事后控制”活動。主要是通過對操作者開展設(shè)備點檢要素的針對性培訓(xùn)教育,開展專項點檢,提高員工專業(yè)能力的活動。
4、設(shè)備故障源未納入點檢標(biāo)準(zhǔn)、未進行設(shè)備點檢、點檢結(jié)果和實際不符視為不能保證設(shè)備的點檢效果。
第四階段:點檢效率化
1、點檢效率化是指:操作者經(jīng)過前四個階段的培訓(xùn)與實踐,對自己操作的設(shè)備性能狀況已有了較深層次的理解,這時員工就有了自己發(fā)現(xiàn)問題的能力,從操作者的角度重新審視前階段制定的清掃、總點檢標(biāo)準(zhǔn),確認點檢項目進行簡單化和優(yōu)化已經(jīng)成為可能。在遵守前階段標(biāo)準(zhǔn)的基礎(chǔ)上進行改進,不斷完善、簡化、優(yōu)化點檢的方法和項目的活動就是點檢效率化。
2、點檢效率化的作用:完善點檢標(biāo)準(zhǔn)、提高點檢工作的效率和精度、減少點檢失誤、提高員工的改善技能、提高員工滿意度,降低設(shè)備故障、為員工自主管理打下基礎(chǔ)。
3、點檢效率化的推行的4個方面:1、點檢內(nèi)容的完善、簡化和優(yōu)化;2、點檢全面目視管理活動的開展;3、設(shè)備故障率的有效管理;4、點檢效率化改善工作的開展。
4、創(chuàng)新目視化:除了規(guī)定的各類儀表,液位,管路,各類表格的目視化,員工在點檢過程中,運用自己的經(jīng)驗,做出能提高點檢效率,提高點檢精度的目視化內(nèi)容。如:日常點檢項目的目視、故障源納入點檢項目后的目視等。
5、標(biāo)準(zhǔn)優(yōu)化:點檢標(biāo)準(zhǔn)和點檢表的修改周期是三個月,在檢查過程中,必須依照設(shè)備科長判定的《點檢標(biāo)準(zhǔn)修訂意見書》上內(nèi)容和點檢標(biāo)準(zhǔn)上的內(nèi)容進行檢查。對修訂的標(biāo)準(zhǔn)因未到修改周期,點檢表上可不體現(xiàn),但現(xiàn)場必須按標(biāo)準(zhǔn)開展,否按不合格評價。
第五階段:自主管理
1、自主保養(yǎng)管理活動是以制造部門為中心的操作者的活動。通過維持設(shè)備的基本條件(清掃、
注油、緊固)、遵守使用條件,根據(jù)總點檢來進行劣化的復(fù)原,把“培養(yǎng)熟悉設(shè)備的工程師”作為目標(biāo),通過階段程序展開教育、訓(xùn)練和實踐的PDCA循環(huán)來實現(xiàn),是操作者按照自己制定的基準(zhǔn)來維持管理現(xiàn)場和設(shè)備的活動就叫做自主管理。
2、自主點檢的目的是重新檢討清掃、加油點檢基準(zhǔn)整理自主保全基準(zhǔn)。為確實做到自主保全基準(zhǔn)的維護管理,設(shè)備提升自主點檢作業(yè)的效率化與目視管理、防止措施等。
3、自主維護需要(1)強化初期清掃,鞏固后再開始后續(xù)活動;(2)開展班組互檢和評比,車間抽檢相結(jié)合;(3)簡化工作流程和表格,減少形式化;(4)激勵措施,調(diào)動一線員工的積極性;(5)加強培訓(xùn),提高員工技能;(6)采取可視化的手段,減輕工作量;(7)開展示范線和樣板機臺活動。
(3)目視管理
1、利用形象直觀、色彩適宜的各種視覺感知信息來組織現(xiàn)場生產(chǎn)活動,達到提高勞動生產(chǎn)率的目的一種管理方法稱為目視化管理。
2、目視管理是利用形象直觀、色彩適宜的各種視覺信息以及感知信息來組織現(xiàn)場生產(chǎn)活動,以達到提高勞動生產(chǎn)率的一種管理方式。目視管理是看得見的管理,即能夠讓員工用眼看出工作的進展?fàn)顩r是否正常,并迅速地做出判斷和決策。
3、可視化管理的作用:使管理更加透明;讓管理更加簡明;使?jié)撛诘膯栴}亮明。
4、應(yīng)用目視化管理技術(shù)的目的是引導(dǎo)操作者正確行為,預(yù)防失誤操作。
5、目視化管理的好處:識別標(biāo)識和地點、生產(chǎn)狀態(tài)、標(biāo)準(zhǔn)作業(yè)流程、業(yè)績信息、改變與改善。
6、看板管理的六大好處:明確管理狀況,營造有形及無形的壓力,有利于工作的推進、營造競爭的氣氛、營造現(xiàn)場活力的強有力手段、展示改善的過程,讓大家都能學(xué)到好的方法及技巧、展改善成績,讓參與者有成就感、自豪感、樹立良好的企業(yè)形象。
7、開展全員可視化管理活動需要
1)、設(shè)定目標(biāo)、明確目的;
2)、建立開展的組織、推選負責(zé)人;
3)、要有計劃,全面考慮和設(shè)計對象;
4)、確定可視化管理的項目;
5)、研究展開的方法和表現(xiàn)的形式;
6)、按計劃,組織可視化活動的實施;
7)、實施效果的追蹤、改進和提高。
8、可視化管理工具有顏色、標(biāo)簽、標(biāo)牌、實物、看板、圖表、照片、電子媒體、燈箱等。
9、安全色分別是:紅色:表示禁止、停止藍色:表示指令綠色:表示提示黃色:表示警告
10、水蒸氣管道的顏色應(yīng)為大紅色
11、空氣管道的顏色應(yīng)為灰色
12、氮氣氣瓶應(yīng)為黑色
建立生產(chǎn)有序、管理順暢,操作規(guī)范,士氣高昂、高質(zhì)量、低成本、短交期的作業(yè)現(xiàn)場;
為企業(yè)規(guī)劃設(shè)計一套由內(nèi)到外的形象升級,外觀視覺價值體現(xiàn)、內(nèi)在的管理內(nèi)涵體現(xiàn);
全員參與設(shè)備管理高產(chǎn)出和低成本運營,提升設(shè)備管理能力,維護能力,提高效率
構(gòu)建班組生產(chǎn)管理體系、循環(huán)評價、人才育成、持續(xù)改善、績效管理、文化養(yǎng)成體系;
提高產(chǎn)品質(zhì)量、降低生產(chǎn)成本、縮短交期、增加利潤,讓管理更系統(tǒng)科學(xué),執(zhí)行力更強
對工廠的各個組成部分進行合理安排,以提高生產(chǎn)效率、降低成本、優(yōu)化物流、改善工作環(huán)境等